What if There Was a Way to Combine DIY and Professional Construction?
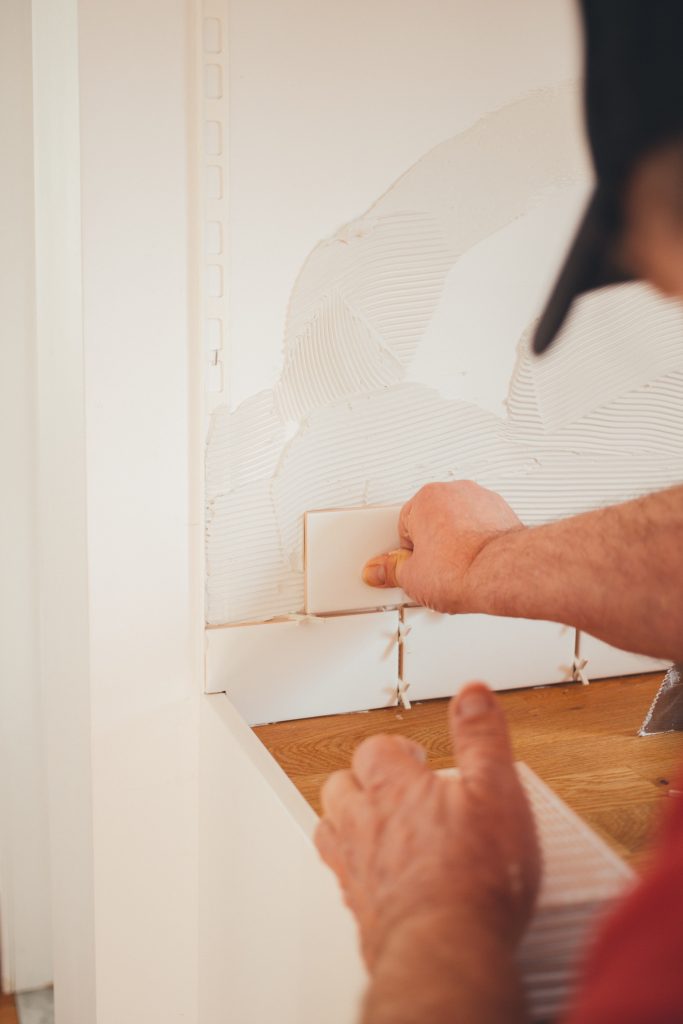
The question is probably more like a billion dollar one. The DIY industry is booming. It’s everywhere we look, TV commercials, internet ads, home improvement programs and online videos. There’s simply a level of pride that goes with doing things ourselves.
Why is the DIY industry so popular and prevalent?
That would be because the construction industry has let too many people down through a whole list of things. These problems certainly are good reasons to consider a DIY project. Here are a few other reasons you might think about doing your own construction project.
Price – is the number one reason for doing your own projects or being your own general contractor. Construction is expensive and the cost of professionals and general contractor’s markups are dollars saved.
The important thing to consider is…
What are the dollars saved costing you?
As a professional I have witnessed too many DIY projects that have gone badly. The experience factor goes a long way to avoid problems. Depending on where you’re located, some construction actions require licensed professionals to do them. You probably wouldn’t stitch up your own gaping wound or represent yourself in court. Not that both haven’t been done, but they come with a risk. The cost of your time spent doing this rather than that, doing things over, unsolved problems or project disasters can be expensive.
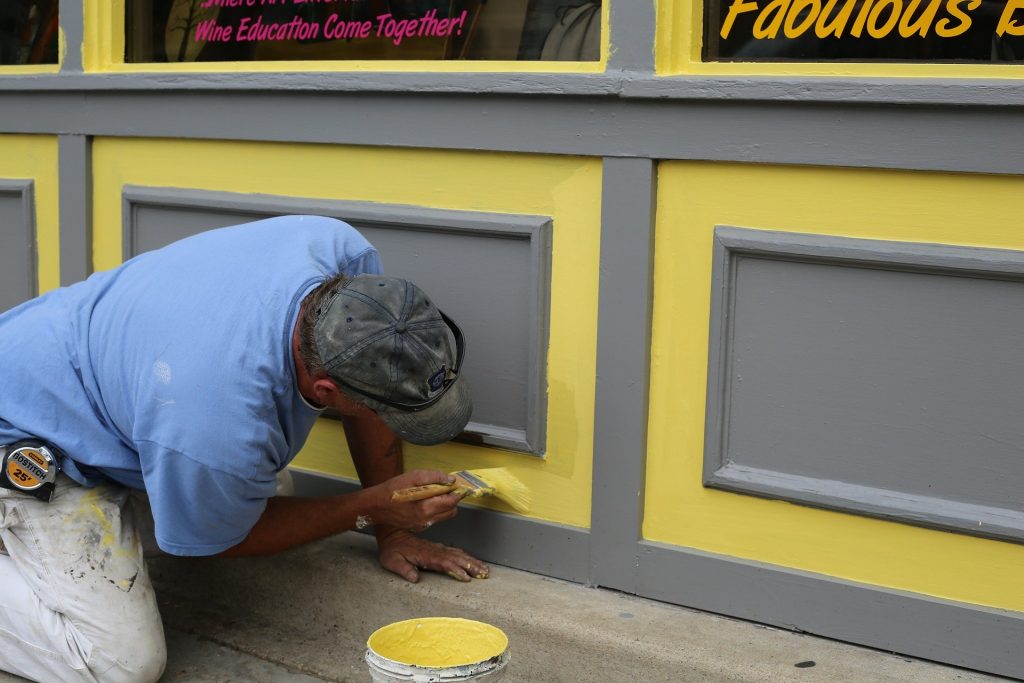
The value of a professional often exceeds the cost.
Control – is another important issue that customers face. The construction industry has one of the worst satisfaction ratings. The only one ranked worse is the used car business. In too many cases customers have felt out of control. This makes it understandable why you would prefer to not deal with contractors. There is a comfort that comes from being in control of the project even with little or no experience.
Sense of accomplishment – is one of the best feelings that we experience. This feeling is especially connected with seeing a physical achievement. Stepping back and looking at something we built is satisfying. These are legitimate reasons you might consider doing your own construction project.
What if there was a way to do your own project while having access to professional experience, knowledge, and connections?
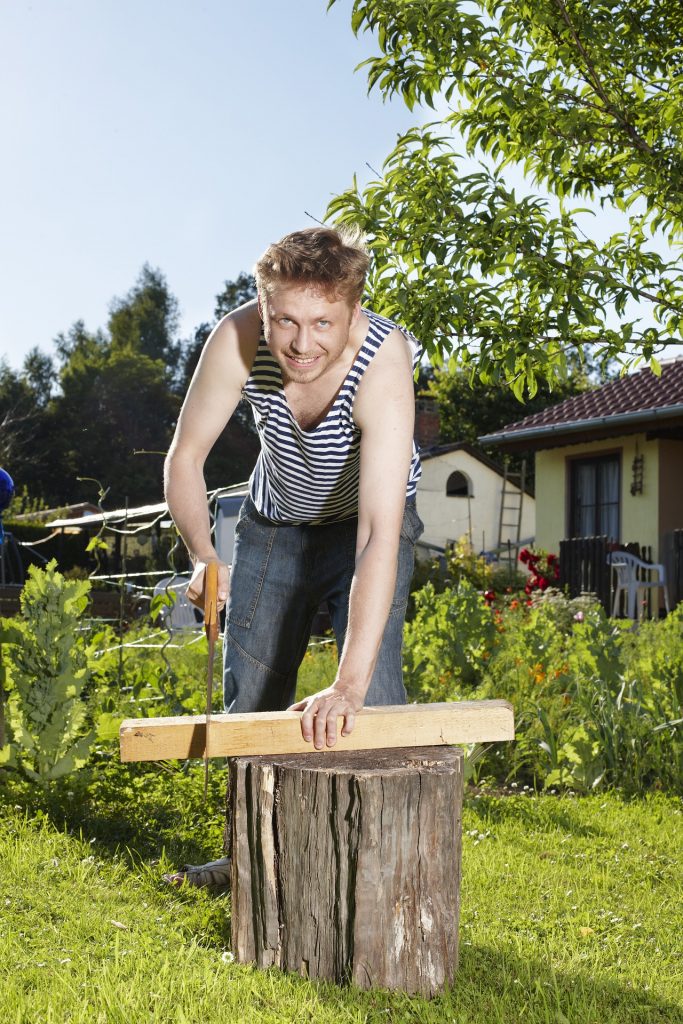
Wouldn’t this be great. This would be a win – win. If there was such a plan out there. What would something like this even look like? What would it include?
You might say, “There’s already services out there for connecting me with construction services. I can contact Angie’s List or Home Advisor.” The problem with these services is, the list of companies and individuals they provide to you, pays to be on the list. I know because they’re calling me regularly wanting me to pay dues and join. This isn’t the most reliable resource.
I’m considering something that would be more detailed and customizable. A service that would fit your individual needs. A mix of educating, advising, consulting. Something that would allow you to have your questions for your project answered.
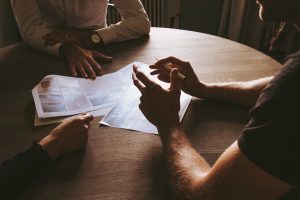
This would allow you to “do it yourself” with the benefit of professional guidance.
As we research this service, we need your help. Give us your thoughts by taking this short survey or leaving comments below.