And How This Can Affect Your Home Maintenance
Sometimes the changing seasons can be quick and serious. The weather here has been a bit of a roller coaster ride over the past several weeks. We’ve had temperatures ranging from below zero to seventy. Some of these swings have happened within days.
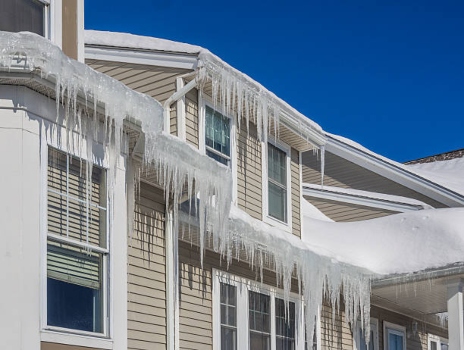
It’s currently seventeen degrees on midday Friday as I’m writing this. It’s predicted to be in the upper sixties by Monday. On the other side of this extreme, we had a low temperature of five degrees below zero this past Wednesday.
When the temperature gets down into single digits there is the concern of freezing water lines. This can lead to broken pipes and water damage. With proper preparation and planning these problems can be reduced.
This is where a home maintenance plan comes in.
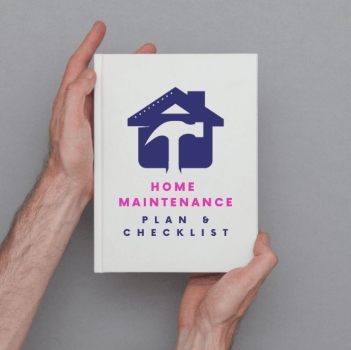
Too often we get busy with life and forget to prepare for seasonal changes when it comes to our homes. We are creatures of habit. We perform our daily routines of coming and going and rarely bother to look around. Unless a doorknob falls off in our hand, or there’s no hot water for our shower, or the sink gets stopped up, or the AC doesn’t work, or any number of other problems occur, we just go through life without giving any thought to the maintenance of our homes.
Maintenance isn’t going to prevent every big problem from happening, but it decreases the likelihood. Having a scheduled maintenance plan will also help you find the needed repairs before they become major.
Having an intentional plan is important, but it won’t work if you don’t use it.
With everything else going on in life, how can we remember one more thing? We don’t have to if we have a scheduled plan. First, you need to decide if home maintenance is important enough for you to bother with. If you’re okay dealing with big problems, then don’t worry about maintenance. You’ll know that the pipes are frozen when you don’t have water at the faucet or there’s water spraying out of the broken pipe.
Because I live in an old family home that was built in 1916, there are still areas that have no insulation. It so happens that one of those areas is where the plumbing is. This means that part of my maintenance plan includes – stacking bales of hay along the north wall of the house and having a thermostat-controlled heat lamp in the crawlspace. The point of this is that if I don’t remember to take the precautions and the weather gets cold, I’ll more likely than not, have frozen pipes. That’s why this is part of my home maintenance plan.
Routine maintenance is a good way to minimize costly disruptions.
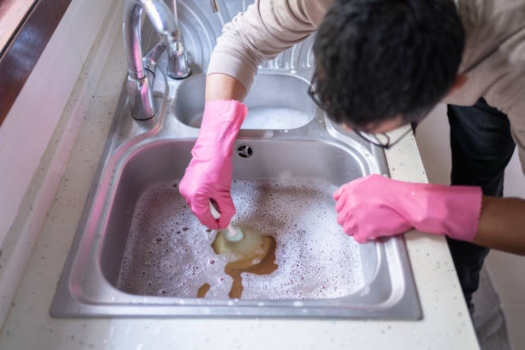
Seasons happen every year and are a natural part of life. Each season presents different weather conditions and temperatures which affect your home in varying ways. Combining a calendar and a seasonal Home Maintenance Checklist helps minimize bigger problems. This plan is broken down into monthly, quarterly, and annually by season.
Just like it’s cold right now—but expected to fifty degrees warmer in a few days—the seasons are the same way. It will be Spring before you know it and there are things that will need to be done.
Get your free Home Maintenance Plan and start taking care of your home maintenance today.